AN IIDEAL DELIVERY, A DIFF-ERENT APPROACH AND GETTING A SHIFT ON.
This week's blog starts with a huge thank you to our long time partner, IIDEA Ltd. The recent delivery of the 2019 hubs has contributed to the progression towards a rolling chassis as we march towards FSUK 2019. Further deliveries of Bodywork and in house manufacturing developments are keeping the team on course for their earliest build completion to date! Read on to find out more!
A GREAT IIDEA COMES TO LIFE
Having partnered with the team for the past 5 years, IIDEA have been a centre point of the continuing success of the team as it moves from strength to strength. This year, IIDEA have used their excellence in machining and design consultancy to help our 'WHUBS' manager, Samuel Seabrooke, create a component which is not only lightweight and optimised for its function, but is also easily machinable.

The 2019 hubs, for the first time, feature a hollow running shaft, utilising a single locking nut to retain the front sets, and the attaching Constant Velocity joint to bring together the driven wheels. Made from Titanium, the hubs save 300g from their steel counterparts, and 230g over 2018's set. Not only has overall weight been reduced, but the Design for Assembly (DfA) aspect has improved, with the brake rotor now able to be removed without disassembly of the entire Upright assembly.

IIDEA Ltd. are not only a supporter of the team's technical advancements, but also in the team members themselves, working with the young engineers to develop their design and commercial awareness skills. IIDEA are currently supporting students on placement at their Sheffield/Rotheram AMRC based site.
SHU Racing would like to thank IIDEA Ltd. for their continuing support, and their commitment to train the next generation of engineers in the Sheffield City Region.
MOUNTS, WITH A DIFF-ERENCE
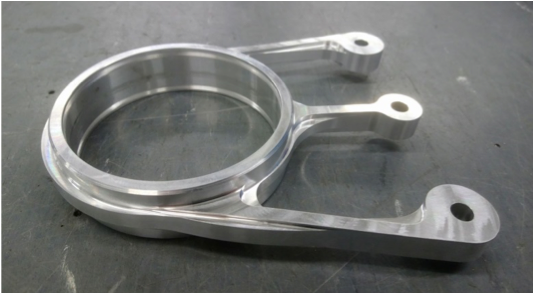
A main focus of the powertrain manager this year, David Gray, was to ensure the engine is aligned correctly in the chassis during manufacture. Key to this is the differential mounts, manufactured in-house by our very own technicians.
Fresh off the CNC mill is one of these new super lightweight mounts. Manufactured from Aerospace grade 7000 series aluminium, David's designs offer a significant weight saving over their 2018 counterparts.
The first of the pair has been manufactured and weighs 226g, compared to the 2018 mounts which weight 422g, providing a 46% weight reduction. Fun Fact: David's differential mount weight savings have followed a perfect quadratic trend from when he designed his first mounts in 2014!
STEPPING UP A GEAR

One of the key issues that was highlighted by our development driver, Oliver Mitchell, was the 2018 car's difficulty to change gear. To rectify this, Ollie has worked with the chassis manager, Martin Heathcote, and the Electrical Manager, Jordan Waite, to retrofit a solenoid shifter and a paddle shifter mechanism to the 2018 car.
This system will be tested over the upcoming weeks before being added to the 2019 car at a later date. We have also been able to take advantage of the great rapid prototyping and printing facilities on offer at Sheffield Hallam University to sinter the Solenoid bracket and paddle shifters.